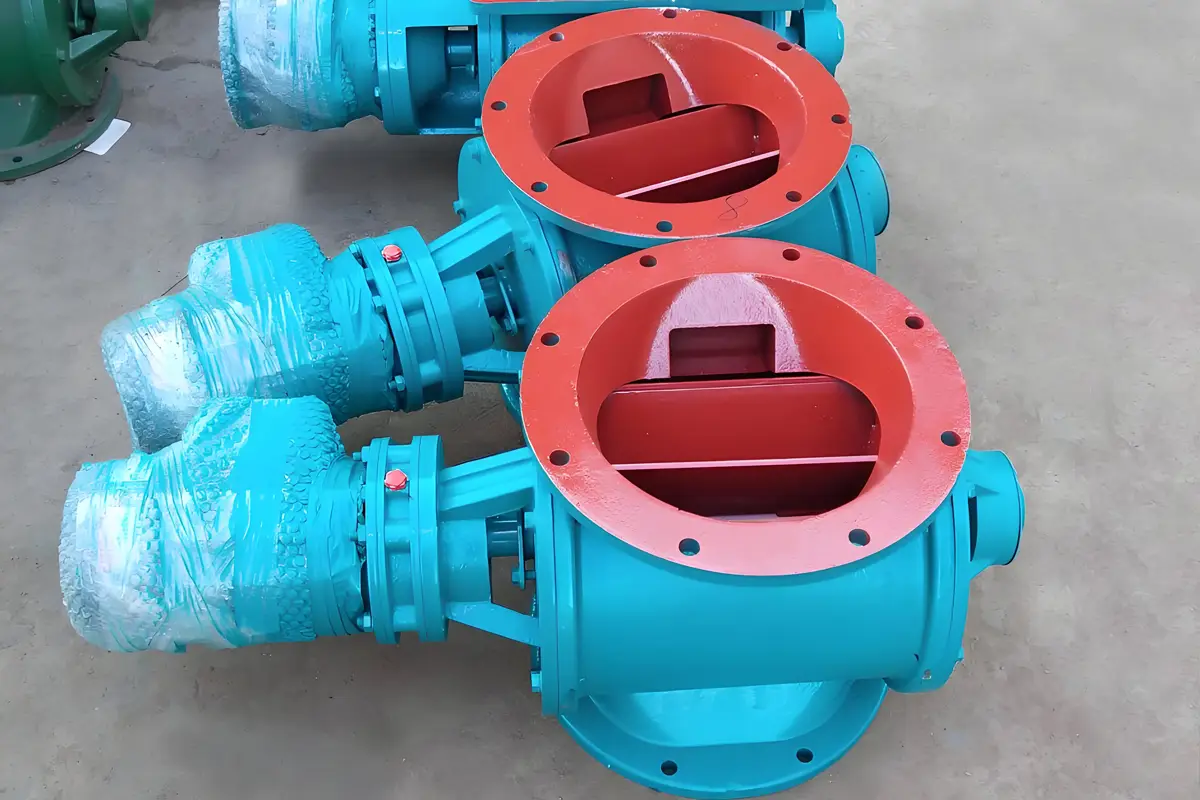
The Ultimate Guide to Rotary Valves: Types, Functions & Applications
What Is a Rotary Valve?
A rotary valve (also called a rotary feeder or rotary airlock) is a critical component in powder, granule, and bulk material handling systems. It ensures precise discharge, metering, dust control, and pneumatic conveying in industries ranging from food processing to cement manufacturing.
How Does a Rotary Valve Work?
Rotary valves operate via a simple yet efficient mechanism:
A motor-driven rotor with multiple vanes rotates inside a housing.
Material from the hopper fills the vane chambers as they pass the inlet.
The rotor turns, transporting material to the discharge point for controlled release.
This process ensures consistent, uninterrupted material flow, making rotary valves ideal for gravimetric or volumetric feeding.
Key Features & Benefits of Rotary Valves
✔ Wide Temperature Range – Handles materials from 0°C to 500°C (depending on model).
✔ Adjustable Feed Rate – Speed control via variable frequency drives (VFDs) for precise dosing.
✔ Excellent Air Locking – Minimizes pressure loss in pneumatic conveying systems.
✔ Low Material Degradation – Gentle handling preserves particle integrity.
✔ Durable & Low-Maintenance – Simple design ensures long service life.
Where Are Rotary Valves Used? (Common Applications)
Rotary valves are essential in industries requiring controlled material flow, including:
✅ Chemical & Pharmaceutical – Precise ingredient dosing, dust containment.
✅ Food & Beverage – Hygienic handling of powders, grains, and additives.
✅ Cement & Construction – Reliable discharge from silos and mixers.
✅ Plastics & Recycling – Feeding pellets, flakes, and regrind materials.
✅ Energy & Environmental – Biomass handling, fly ash removal, and more.
Disadvantages of Rotary Valves
While highly efficient, rotary valves have some limitations:
❌ Wear with Abrasive Materials – Hard particles can degrade vanes over time.
❌ Potential for Material Leakage – Requires proper sealing for fine powders.
❌ Not Ideal for Sticky Materials – May cause clogging without special designs.
Solution: Choosing the right valve type (e.g., wear-resistant, anti-jamming, or sanitary models) minimizes these issues.
Types of Rotary Valves & Their Functions
1. Standard Rotary Feeder Valve
- Function: Basic material discharge & airlock sealing.
- Applications: General powder & granule handling.
2. High-Temperature Rotary Valve (Up to 500°C)
- Function: Handles hot materials (e.g., cement, ash).
- Key Feature: Heat-resistant seals & alloys.
3. High-Pressure Rotary Valve (0.6 MPa Max)
- Function: For dense-phase pneumatic conveying.
- Key Feature: Reinforced housing & pressure relief.
4. Anti-Jamming Rotary Valve
- Function: Prevents material bridging & blockages.
- Key Feature: V-shaped inlet & optimized vane design.
5. Wear-Resistant Rotary Valve
- Function: Handles highly abrasive materials (e.g., sand, minerals).
- Key Feature: Hardened surfaces or ceramic coatings.
6. Sanitary Rotary Valve (Food/Pharma Grade)
- Function: Meets hygienic standards (FDA, EHEDG).
- Key Feature: Smooth surfaces, easy cleaning, #400 polish.
How to Choose the Right Rotary Valve?
When selecting a rotary valve, consider:
🔹 Material Type (powder, granules, abrasive, sticky?)
🔹 Temperature & Pressure Requirements
🔹 Flow Rate & Precision Needs
🔹 Industry-Specific Standards (food-grade, explosion-proof, etc.)
Looking for a Reliable Rotary Valve Manufacturer?
Darko is a leading rotary valve supplier, specializing in custom solutions for various industries. Our valves ensure:
✔ High Efficiency – Smooth material flow with minimal leakage.
✔ Durability – Robust construction for long-term performance.
✔ Customization – Tailored designs for unique applications.
Need a rotary valve? Contact ustoday for expert advice & solutions!