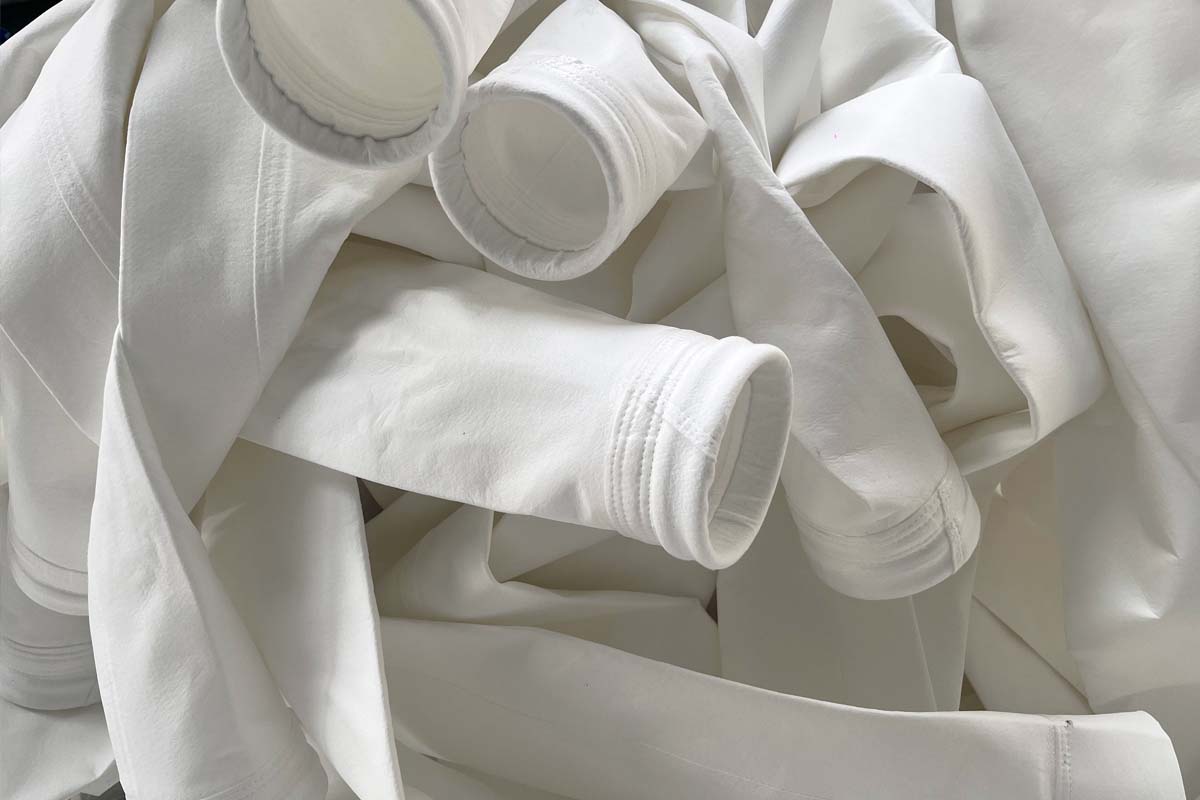
Filter Bags: The Unsung Heroes of Industrial Cleanliness and Efficiency
Introduction: More Than Just a Fabric Sack
In the complex world of industrial processes, maintaining air and liquid purity isn’t just about regulatory compliance; it’s about product quality, equipment longevity, operational efficiency, and worker safety. At the forefront of this battle against contaminants stands a seemingly simple component: the filter bag. These specialized fabric or felt sleeves are far more sophisticated than they appear, playing a pivotal role in countless applications across diverse industries. This article dives deep into the world of filter bags, exploring their types, materials, applications, benefits, and key selection considerations.
What Exactly is a Filter Bag?
At its core, a filter bag is a permeable container, typically cylindrical or pocket-shaped, designed to capture solid particulate matter from a gas (e.g., air, exhaust fumes) or liquid (e.g., water, chemicals, paints) stream as it passes through the fabric’s matrix. They operate on a principle called surface filtration: as contaminated fluid flows through the bag, particles larger than the pore size of the filter media get trapped on the surface or within the depth of the fabric, allowing the cleaner fluid to pass through.
They are the primary filtration element within a baghouse (for air/gas) or a bag filter housing (for liquids). These housings provide structural support, ensure a proper seal, and facilitate the cleaning or replacement process. The efficiency and lifespan of the entire filtration system hinge heavily on the quality and suitability of the filter bag itself.
Key Types of Filter Bags
Filter bags can be broadly categorized based on their application:
1.Dust Collection Bags (Air/Gas Filtration): Primarily used in baghouse dust collectors. These are essential for:
- Industrial Air Pollution Control: Capturing dust, fumes, and particulates from manufacturing processes (cement, metalworking, woodworking, food processing, pharmaceuticals, chemicals).
- Material Recovery: Reclaiming valuable product powders (e.g., flour, sugar, pigments, plastic pellets).
- Process Air Filtration: Ensuring clean air enters or recirculates within sensitive processes (paint booths, clean rooms).
2.Liquid Filter Bags: Designed for immersion in liquid streams within pressure vessels (bag filter housings). Applications include:
- Coolant and Process Fluid Filtration: Removing contaminants from metalworking coolants, wash water, plating baths, and process chemicals.
- Pre-filtration: Protecting finer filters (e.g., cartridges, membranes) in water treatment, chemical processing, and food & beverage production.
- Paint Filtration: Ensuring paint particles are removed before spraying.
- Solvent Filtration: Cleaning solvents for reuse.
- General Water Filtration: Treating process water, effluents, or intake water.
The Material Makes the Difference: Filter Bag Media
The choice of fabric is critical, dictating filtration efficiency, chemical compatibility, temperature resistance, and durability. Common filter bag materials include:
- Polyester (PET): Excellent general-purpose material. Resistant to moisture, abrasion, and common chemicals. Cost-effective with good temperature resistance (up to ~135°C / 275°F continuous). Widely used in dust collection and liquid filtration.
- Polypropylene (PP): Excellent chemical resistance, especially to acids and bases. Naturally hydrophobic (water-repellant), making it ideal for wet processes or moisture-laden gas streams. Lower temperature limit (~80-90°C / 176-194°F). Common in liquid filtration and mildly corrosive dust collection.
- Nomex (Aramid): Excellent high-temperature resistance (up to ~200°C / 392°F continuous). Good abrasion resistance. Used in high-heat applications like asphalt plants, foundries, kilns. Susceptible to hydrolysis (damage from moisture) if gas temperatures drop below dew point.
- PPS (Ryton / Polyphenylene Sulfide): Excellent chemical resistance, especially to acids and bases, and high thermal stability (up to ~190°C / 374°F). Highly resistant to hydrolysis. Ideal for coal-fired boilers, chemical processes, and waste incineration.
- PTFE (Teflon / Polytetrafluoroethylene): Exceptional chemical resistance (virtually inert), non-stick properties (easy cake release), and high thermal stability (up to ~260°C / 500°F). Used for aggressive chemical processes, demanding dust applications, and situations requiring superior cake release. Membrane lamination is common to enhance efficiency.
- Fiberglass: Excellent high-temperature resistance (up to ~260°C / 500°F continuous). Used primarily in high-heat applications like cement kilns, glass furnaces. Requires careful handling to avoid damage; often treated with protective coatings (e.g., PTFE, silicone).
- Cotton: Natural fiber used historically and occasionally now for certain non-demanding, low-temperature dust collection tasks. Less durable and efficient than synthetics.
Manufacturers also enhance fabrics using techniques like calendering (smoothing to create a finer surface finish), singeing (burning off loose fibers), and applying PTFE membrane coatings (creating a true surface filter with extremely high efficiency at the surface).
Design Variations: Pleated vs. Non-Pleated
- Standard Non-Pleated Bags: The traditional design for both dust collection and liquid filtration. Surface area per bag is determined by bag length and diameter.
- Pleated Filter Bags: Increasingly popular, especially in dust collection. Featuring accordion-like pleats, these bags significantly increase the available filtration surface area within the same housing footprint compared to a standard bag. This translates to:
- Higher airflow capacity per bag.
- Reduced pressure drop (energy savings).
- Longer bag life (due to larger dust cake surface area and potentially lower face velocity).
- Smaller equipment footprint for the same duty. Often made with durable, rigid media like PTFE-coated fabrics.
Why Choose Filter Bags? Key Advantages
- High Efficiency: Modern filter bags, especially those with membranes or fine felt structures, can achieve very high capture efficiencies for fine particles, often sub-micron.
- Large Particle Holding Capacity: Can handle large volumes of dust or debris before requiring cleaning or replacement.
- Cost-Effectiveness: Generally offer a lower initial cost and operating cost per unit of filter media compared to cartridges or other fine filters in many applications. Bag replacement is straightforward.
- Versatility: Available in numerous materials and designs suitable for an extremely wide range of temperatures, chemical exposures, and particle types.
- Durability: Engineered synthetic and coated fabrics offer long service lives under appropriate operating conditions.
- Reusable (Liquid Bags): Many liquid filter bags are disposable, but some heavier-duty designs are cleanable and reusable.
- Reliability: Proven technology that, when sized and applied correctly, offers reliable, continuous operation.
Selecting the Right Filter Bag: Critical Factors
Choosing the optimal filter bag is crucial for performance and cost-effectiveness. Consider:
- Application: Air/gas dust collection or liquid filtration? This defines the housing type and cleaning mechanism.
- Particle Size & Type: Determines the required micron rating and media selection (e.g., membrane for fine particles). Is the dust abrasive, hygroscopic, sticky?
- Fluid Properties:
- Air/Gas: Temperature, moisture content (dew point), chemical composition (corrosives, oxidizers).
- Liquid: Chemical composition, pH, viscosity, temperature.
- Concentration: Dust or particulate load significantly impacts cleaning frequency and bag life.
- Operating Conditions: Continuous vs. batch processing, flow rates, pressure drop limitations.
- Required Efficiency: Target level of particle removal (e.g., PM10, PM2.5, absolute rating like 1 micron).
- Cleaning Mechanism (Dust Collectors): How is the dust removed (pulse-jet, reverse air, shaker)? Different bags perform better with different cleaning methods.
- Cost of Media: Balancing initial cost with expected service life and performance efficiency. A cheaper bag that clogs quickly or fails prematurely is more expensive long-term.
Maintenance and Lifespan: Maximizing Filter Bag Performance
Filter bag longevity and system efficiency rely heavily on proper maintenance:
- Regular Inspection: Visual checks for tears, abrasion, coating damage, or improper installation.
- Monitoring Pressure Drop: Increasing differential pressure indicates filter loading or blinding. Monitor for trends indicating premature failure.
- Correct Cleaning (Dust Collectors): Optimize cleaning parameters (pulse pressure, duration, interval) to effectively shed the dust cake without damaging the bag or pushing dust deeper into the fabric.
- Preventing Baghouse Problems: Avoid dew point condensation (leads to blinding & bag damage). Ensure proper air-to-cloth ratio (design airflow per square foot of filter media). Address inlet distribution issues causing uneven wear.
- Timely Replacement: Replace bags when efficiency drops significantly, pressure drop remains excessively high after cleaning, or physical damage occurs. Always replace full sets according to the system manufacturer’s recommendations to maintain even airflow.
- Proper Installation: Seals must be airtight (gas) or watertight (liquid). Sealing cages must be intact and undamaged. Bags should hang freely without folds or creases that hinder cleaning or flow.
Conclusion: The Essential Element
The filter bag remains an indispensable component in the pursuit of industrial efficiency, environmental responsibility, and quality control. From the towering stacks of power plants to the precise nozzles of paint lines, from food processing plants to pharmaceutical clean rooms, these durable fabric barriers silently perform a critical function. Understanding the diverse types, sophisticated materials, and key selection factors allows engineers, maintenance personnel, and facility managers to optimize their filtration systems. Investing in the right filter bag and maintaining it properly leads to reduced operating costs, extended equipment life, improved product quality, compliance with environmental regulations, and ultimately, a safer, cleaner work environment. When the goal is purity and efficiency, choosing the right filter bag is truly foundational.