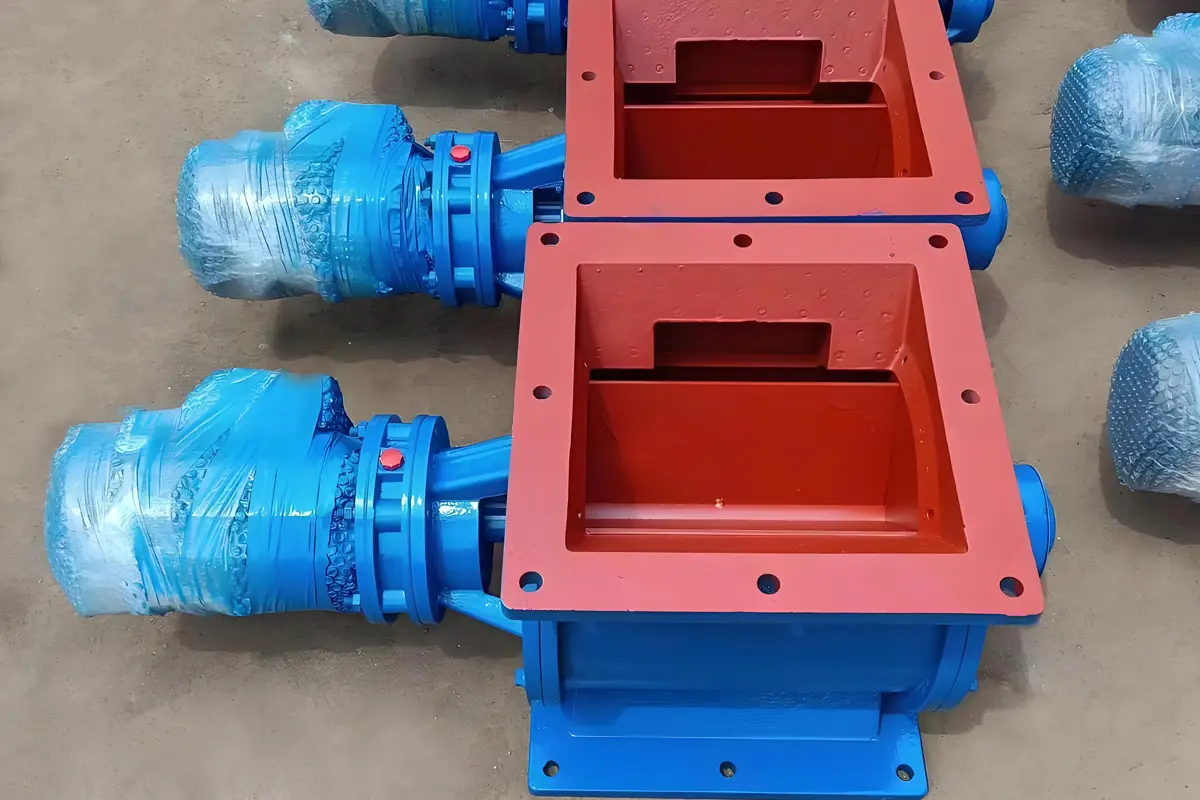
Rotary Valve Technology: Core Principles & Maintenance
Introduction: The Unsung Heroes of Industrial Flow Control
In the intricate world of industrial automation and bulk material handling, countless components work silently together. Among the most crucial, yet often overlooked, is the rotary valve, also known as a rotary airlock or rotary feeder. This ingenious device acts as a critical seal and metering mechanism, ensuring smooth, efficient, and controlled transfer of powders, granules, pellets, and other bulk solids between process stages – often between environments operating at different pressures. For industries ranging from food and pharmaceuticals to plastics, chemicals, and energy, rotary valves are indispensable for maintaining process integrity, minimizing product loss, and preventing atmospheric contamination. Their reliable operation, however, hinges on consistent, clean electrical power – precisely where voltage stabilizers become an essential partner in maximizing uptime and protecting your investment.
What is a Rotary Valve? Function & Core Design
At its simplest, a rotary valve consists of a rotating rotor housed within a precision-machined casing or housing. The rotor features multiple vanes (typically 6, 8, 10, or 12) radiating from a central shaft, creating distinct pockets.
How It Works:
1. Material Intake: As the rotor turns, these pockets fill with material entering from an inlet (usually above the valve).
2. Material Transport & Sealing: The rotating vanes transport the material through the valve body. The close tolerance between the rotor tips and the housing creates a dynamic seal, preventing significant air or gas from passing through the valve alongside the material.
3. Material Discharge: The filled pockets rotate to the outlet (below the valve), where gravity discharges the material.
4. Continuous Flow: The rotation continues, creating a consistent, pulsating flow of material.
Core Objectives: * Air Locking: Prevent unwanted air/gas flow between pressurized or vacuum systems and atmospheric conditions (e.g., between a pneumatic conveyor line and a storage silo). * Material Feeding: Precisely meter or dose bulk solids into downstream processes like conveyors, mixers, reactors, or packaging machines. * Material Discharge: Facilitate controlled gravity flow from hoppers, bins, or cyclones. * Isolation: Act as an isolation point for process sections.
Key Applications of Rotary Valves: Where Precision Meets Power
Rotary valves are ubiquitous in industries handling bulk solids:
- Food & Beverage: Transferring flour, sugar, grains, spices, coffee beans, powders. Hygiene and material integrity are paramount (often requiring washdown designs – SS316L).
- Pharmaceuticals: Handling potent APIs, excipients, granules. Requires ultra-high purity materials (e.g., 316L, polished finishes) and stringent validation (cGMP).
- Plastics & Chemicals: Metering pellets, powders, flakes, catalysts. Often demands robust construction for abrasive materials and resistance to corrosive chemicals.
- Minerals & Cement: Handling highly abrasive materials like fly ash, cement, sand, ores. Emphasizes heavy-duty designs and wear-resistant liners.
- Energy (Biomass, Coal): Feeding biomass pellets or coal dust into boilers or gasifiers. Combustion safety and robust construction are critical.
- Recycling: Handling fragmented plastics, paper, metals.
- Pneumatic Conveying: Essential components at the feed point (blow-through) or discharge point (pressure or vacuum systems).
Critical Performance Factors & Specifications
Selecting the right rotary valve involves careful consideration of several interlinked factors:
- Material Characteristics: Abrasiveness, particle size/shape, bulk density, cohesiveness, temperature, moisture content, explosivity (ATEX certification).
- Valve Size (Housing & Inlet/Outlet): Dictated by required flow rate (Cubic Feet per Hour – CFH / Cubic Meters per Hour – M³H) and connection dimensions.
- Rotor Type: Open-ended, closed-ended, shallow pocket, star-shaped, variable pitch, coated, lined. Impacts material handling capability, sealing efficiency, and cleanability.
- Housing Construction: Cast iron, carbon steel, stainless steel (304, 316, 316L), specialized alloys. Choice depends on material compatibility, corrosion resistance, hygiene requirements, and weight.
- Sealing System: Shaft seals (lip seals, mechanical seals, packing glands) and rotor tip clearance/contact. Critical for preventing leakage and maintaining pressure differential.
- Drive Mechanism:
- Electric Motor: The most common drive. Offers precise speed control. Requires stable voltage for consistent torque and RPM.
- Gearmotor: Reduces motor speed to the required output RPM. Vulnerable to damage from voltage fluctuations causing torque spikes.
- Shaft Coupling: Transfers torque from the gearmotor to the rotor shaft.
- Bearings: Positioned on either end of the rotor shaft to support rotation. Misalignment or vibration caused by erratic power can accelerate bearing failure.
Why Consistent Electrical Power is Non-Negotiable for Rotary Valve Reliability
The drive system – specifically the electric motor and gearbox – is the lifeblood of a rotary valve. This is where the quality of your facility’s electrical power directly impacts performance, longevity, and maintenance costs:
Advantages: Why Choose a Bucket Elevator?
- Precise Speed Control & Metering Accuracy: Fluctuating voltage can cause motor speed variations. Even minor changes in RPM significantly impact the volume of material discharged per revolution. Voltage stabilizers ensure constant motor speed for accurate batching and consistent feed rates, crucial for product quality and process efficiency.
- Protecting Sensitive Electronics & Drives: Modern valves often incorporate Variable Frequency Drives (VFDs) for speed control, or sensors for monitoring. These sophisticated electronics are highly susceptible to damage from surges, sags, and harmonics. Stabilizers condition power, filtering out harmful transients that can fry circuit boards and sensors, leading to costly downtime and replacements.
- Preventing Motor Burnout & Reducing Heat: Under-voltage forces motors to draw excessive current to maintain torque, causing overheating and insulation breakdown. Over-voltage stresses motor windings and components. Stabilizers maintain voltage within the safe operating window (typically ±1-2%), preventing thermal overload and extending motor lifespan.
- Minimizing Gearbox & Bearing Stress: Voltage fluctuations cause erratic torque output. Sudden increases can violently jolt the gearbox and rotor, stressing teeth and shafts. Constant fluctuations lead to premature gear wear and bearing fatigue. Clean, stable power ensures smooth torque delivery, protecting mechanical components.
- Reducing Downtime & Maintenance Costs: The cumulative stress of unstable power leads to accelerated wear on motors, gearboxes, couplings, shafts, and seals. This translates directly into unplanned downtime for repairs and increased spare part consumption. A stabilizer investment acts as preventative maintenance, significantly reducing overall cost of ownership.
- Ensuring Air Lock Integrity: Pressure differentials across rotary valves demand consistent rotor rotation and tight clearances. Unstable power, causing speed surges or stalls, can compromise the seal, leading to inefficient conveying, dust emissions, or process inefficiencies.
Integration with Voltage Stabilization: Protecting Your Investment
For mission-critical applications or facilities experiencing power quality issues, integrating a dedicated voltage stabilizer specifically for rotary valve motors and associated control panels is a highly cost-effective strategy.
How Voltage Stabilizers Safeguard Rotary Valve Performance: * Eliminate harmful voltage fluctuations (sags, surges, brownouts). * Filter transient voltage spikes from the grid or nearby equipment. * Maintain voltage within the optimal ±1-2% tolerance. * Protect sensitive VFDs, PLCs, and sensors. * Ensure consistent motor speed for accurate metering. * Reduce mechanical stress on the entire drive train. * Prolong motor, gearbox, and bearing life. * Minimize unscheduled downtime and costly repairs.
Rotary Valve Maintenance: Ensuring Longevity
Proactive maintenance is key, especially in demanding environments:
- Regular Inspection: Check rotor clearance, vane condition (wear/bent), seals for leaks, bearings for noise/heat, gearbox oil level/condition.
- Lubrication: Follow manufacturer schedules for bearings and gearbox.
- Cleaning: Especially critical for sticky or hygroscopic materials to prevent buildup affecting rotation or sealing.
- Seal Replacement: Replace shaft seals promptly upon signs of leakage to prevent material ingress and bearing damage.
- Clearance Checks: Monitor rotor tip/housing clearance; adjust or re-machine as needed.
- Vibration Monitoring: Unexpected vibration can signal misalignment, bearing failure, imbalance, or drive issues potentially linked to unstable power.
- Drive System Check: Monitor motor temperature and vibration; listen for unusual gearbox noise.
Frequently Asked Questions (FAQs)
Leaks can occur due to several reasons beyond just seals: excessive rotor tip clearance (wear), casing warping due to heat, improper rotor/casing tolerances for the material, severe abrasive wear creating gaps, or clogged rotor pockets creating pressure imbalances. Stable power also plays a role – erratic rotation speed can momentarily compromise the seal’s effectiveness.
Answer: Extremely critical, especially for metering applications. RPM directly determines the volume of material discharged per unit of time. Even small variations cause inconsistencies in batch weights or feed rates. For airlock functions, inconsistent RPM can lead to pressure fluctuations affecting efficiency. Voltage stabilizers are the primary solution for ensuring constant motor speed (RPM) when grid power is unstable.
Common causes include: * Under-voltage conditions forcing the motor to draw higher current. * Overloaded valve (e.g., plugged inlet or outlet causing rotor jam). * Deteriorating bearings increasing friction. * Worn or binding gearbox. * Insufficient ventilation around the motor. * Ambient temperature exceeding motor rating. * Voltage harmonics causing extra heating. Investigating power quality with a stabilizer provider is essential, as under-voltage is a frequent culprit behind thermal stress.
These are specialized plates (often made of hardened tool steel or ceramic composite) attached to the outer edges of the rotor vanes. They provide a sacrificial, highly wear-resistant surface where the rotor makes closest contact (or contact) with the valve housing. They are essential when handling highly abrasive materials like sand, fly ash, minerals, or plastic regrind. They dramatically extend the maintenance interval before rotor/casing wear compromises valve performance. Regular monitoring of clearance remains vital.
Conclusion: Partnering Reliability for Peak Performance
Rotary valves are vital components demanding robustness and precision to perform consistently in harsh industrial settings. Their drive systems are particularly vulnerable to the hidden threat of unstable electrical power. Voltage fluctuations and transients are silent killers of motors, gearboxes, and control electronics, leading to inaccurate feeding, compromised air locks, increased downtime, and spiraling maintenance costs.
Proactively integrating industrial-grade voltage stabilizers into your rotary valve installations is not an added expense; it is an investment in protecting valuable assets and maximizing operational efficiency. By ensuring consistently clean and stable power, you guarantee: * Reliable Metering: Consistent product quality.
* Efficient Air Locking: Optimal pneumatic conveying.
* Extended Equipment Lifespan: Reduced replacement costs.
* Minimized Downtime: Increased production throughput.
* Lower Total Cost of Ownership: Reduced energy waste and maintenance bills.
For voltage stabilizer manufacturers, understanding the critical needs of components like rotary valves allows us to craft truly effective power protection solutions that keep industry moving forward smoothly and reliably. Protect your process, protect your valves, protect your power.